I figured I really should test all this before spending a ton of money on it, so I walked around Home Depot and found a tube with a 1/4″ outside diameter. The only magnetic thing I could find to fit inside was a #16 nail, so I bought some of those.
So I cut out some 1″ square dividers, cut a 1/4″ hole in the middle, put a couple of small holes to run wire through, and put them on the tube:
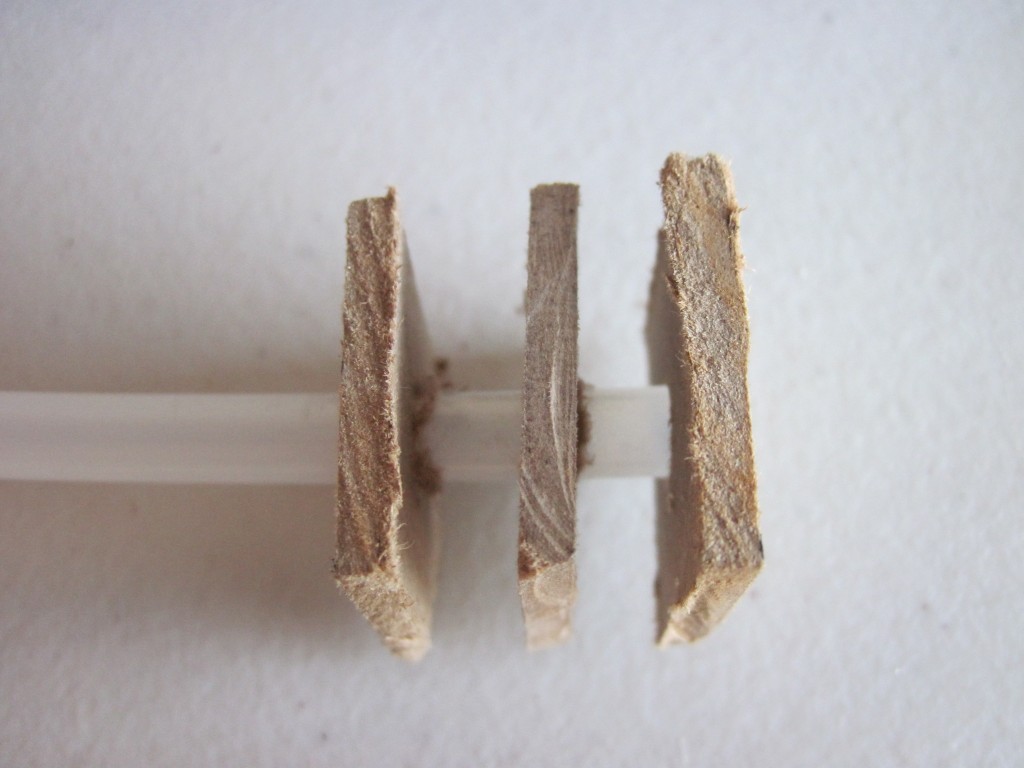
I figured it needed some extra support, so I put superglue around each of the pieces where they attach to the tube.
A couple days later, I tried winding 30 gauge wire on one of them. It worked for a while, but then the end cap popped off. Next I noticed that the middle divider had been moving as well. Clearly the superglue wasn’t holding the dividers. So, I held the endcap on, put a bunch of superglue on the coil to fix that in place and let it sit.

The next day, I stripped the ends of the wire and measured the resistance. It came up right around 5 Ohms, which is just what I was shooting for. This means I can run it up to 20 V, which puts 4 Amps through there. According to a chart I found, 30 gauge wire can take up to 10 Amps for up to 10 seconds, so 4 A shouldn’t be a problem.
This is a perfect use for my new power supply! I hooked the coil up to it, set it for 5 V, saw 1 A going through the coil and played with a nail in the tube. It was certainly getting sucked in, but not very strongly. So, I bumped it up to 20 V and felt the nail get pulled in more strongly. As I played with this a little more, suddenly the coil started smoking. I odor made me think it was actually the superglue burning, but I quickly shut everything down and haven’t touched it again in a week. Hopefully I’ll soon get back to this…